Understanding CNC Machines: A Comprehensive Guide to CNC Machining
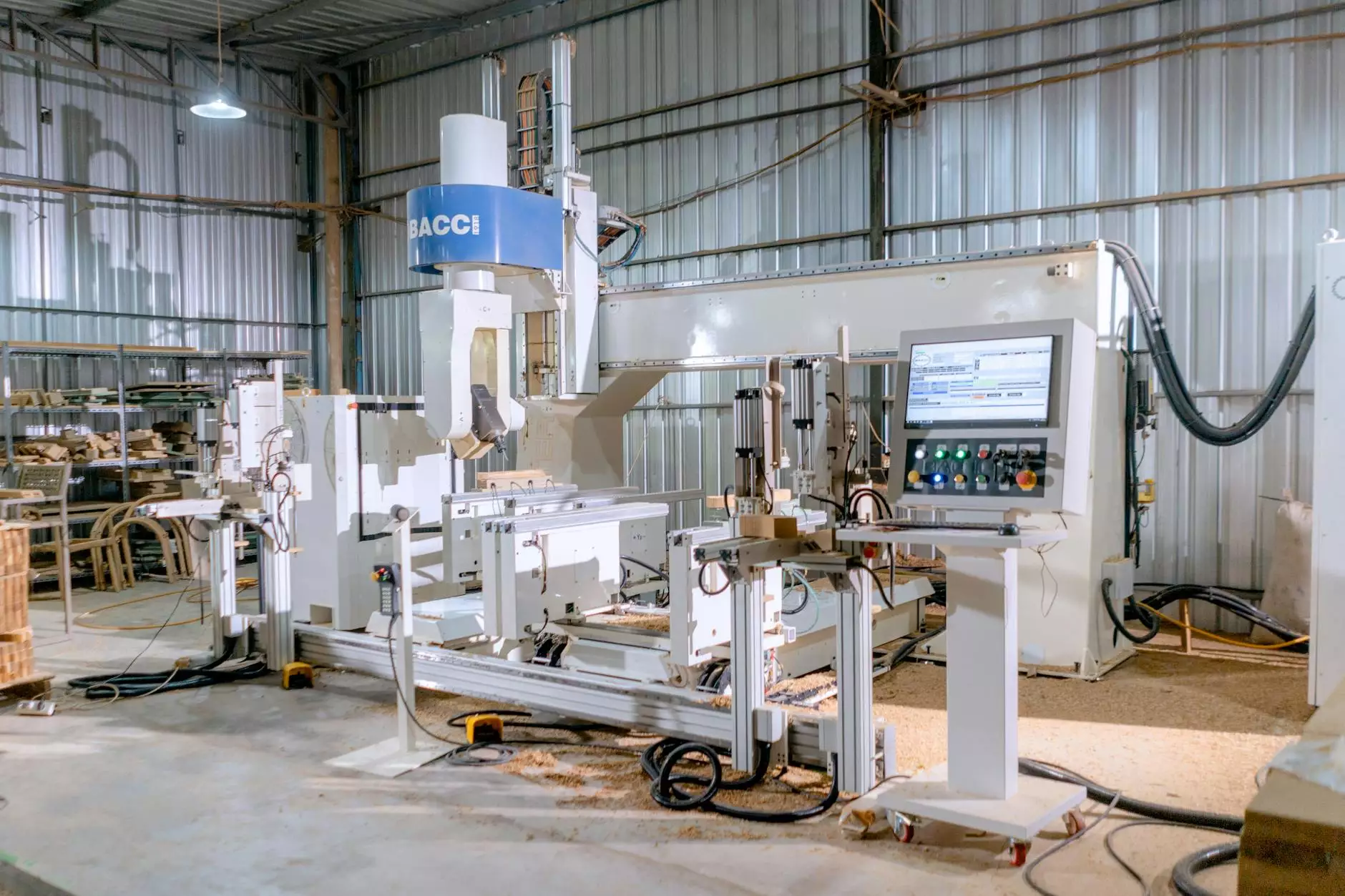
The Evolution of CNC Machines
CNC machines, or Computer Numerical Control machines, represent a significant shift in manufacturing technology. Unlike traditional machinery, which relied on manual operation through handwheels and levers, CNC technology automates the manufacturing process, allowing for improved precision, efficiency, and repeatability.
Early CNC machines emerged in the 1950s, and their evolution has transformed various industries. From aerospace to woodworking, CNC machining has become integral in producing intricate components that demand high accuracy and consistency.
What is CNC Machining?
At its core, cnc machining refers to the process of using computer-controlled tools to create parts from various materials. These machines operate via a pre-programmed sequence of commands, typically written in a language known as G-code.
This method allows for intricate designs to be executed with minimal human intervention, reducing the potential for error and increasing production speed.
How CNC Machines Work
The Role of G-code
G-code, the programming language for CNC machines, plays a crucial role in directing how a machine performs its tasks. Commands in G-code dictate movement, speed, feed rate, and other essential parameters.
For example, a simple G-code command might look like this:
G01 X10 Y10 F150This instruction tells the machine to move to the coordinates (10,10) at a feed rate of 150 units per minute.
Machine Components
A CNC machine comprises several key components, including:
- Controller: The computer that processes G-code and sends commands to the machine.
- Drive System: This includes motors and mechanisms that translate the control signals into physical movements.
- Tool Holder: The part of the machine that holds various tools for cutting, drilling, or milling.
- Workpiece: The raw material being machined.
Types of CNC Machines
There are various types of CNC machines, each designed for specific tasks. Some of the most common include:
- CNC Milling Machines: Use rotary cutters to remove material and produce complex shapes.
- CNC Lathes: Rotate the workpiece against a cutting tool to create cylindrical parts.
- CNC Plasma Cutters: Utilize plasma torches to cut through metal with high precision.
- CNC Laser Cutters: Use lasers for cutting materials with intricate designs.
- CNC Routers: Ideal for carving and detailing in materials like wood, plastic, and foam.
The Importance of CAD and CAM
The effective operation of CNC machines hinges on the use of Computer-Aided Design (CAD) and Computer-Aided Manufacturing (CAM) software.
What is CAD?
CAD software allows designers to create detailed 2-dimensional (2D) and 3-dimensional (3D) models of parts before they are manufactured. By employing CAD, engineers can visualize their designs, identify potential issues, and refine specifications to ensure optimal performance.
What is CAM?
Once the CAD model is complete, CAM software translates the design into a format compatible with CNC machines. This is where the G-code is generated, dictating how the machine will operate to create the part.
The integration of CAD and CAM promotes a seamless transition from design to production, enabling manufacturers to achieve greater efficiency.
The Advantage of CNC Machining
The advantages of CNC machining are extensive and transformative for various sectors. Here are some key benefits:
- Precision and Accuracy: CNC machines can produce parts to tolerances as tight as ±0.005 mm, ensuring consistency across production runs.
- Repeatability: Once programmed, CNC machines can produce thousands of identical parts without variation.
- Automation: Reduces the reliance on manual labor, minimizing human errors and increasing production speed.
- Complex Geometries: CNC machining enables the production of intricate shapes and designs that would be difficult or impossible to achieve manually.
- Material Versatility: CNC machines can work with a wide range of materials, including metals, plastics, wood, and composites.
Challenges in CNC Machining
While CNC machining offers numerous benefits, there are also challenges that manufacturers face:
- Initial Setup Costs: High-quality CNC machines and the required software can be costly investments for businesses.
- Skills Gap: There is a demand for qualified CNC machinists and programmers which can be difficult to fulfill as technology advances.
- Maintenance and Calibration: CNC machines require regular maintenance to ensure optimal performance and prevent breakdowns.
The Future of CNC Machining
As technology continues to evolve, the future of CNC machining is poised to embrace several trends, including:
- Integration of AI and Machine Learning: The use of artificial intelligence to enhance machine learning capabilities and optimize machining processes.
- Advancements in Materials: New materials like composites and advanced alloys could revolutionize what can be manufactured with CNC technology.
- Increased Automation: The continual advancement towards fully automated production lines that require less human oversight.
- Sustainability Efforts: Developing more eco-friendly machining processes and materials as the industry moves toward sustainable practices.
Conclusion
In conclusion, CNC machines have transformed the landscape of modern manufacturing, offering unparalleled precision and efficiency. The integration of CAD and CAM into the workflow enhances production capabilities, enabling manufacturers to produce complex components with remarkable consistency.
Understanding the fundamentals of CNC machining is essential for anyone engaged in manufacturing today. As the industry evolves, staying informed about technological advancements will be critical for success. Embracing CNC machining not only enhances production capabilities but also positions businesses favorably within a highly competitive marketplace.
For more information on CNC machinery, visit Robocon CNC.