The Transformative Power of PBF in 3D Printing
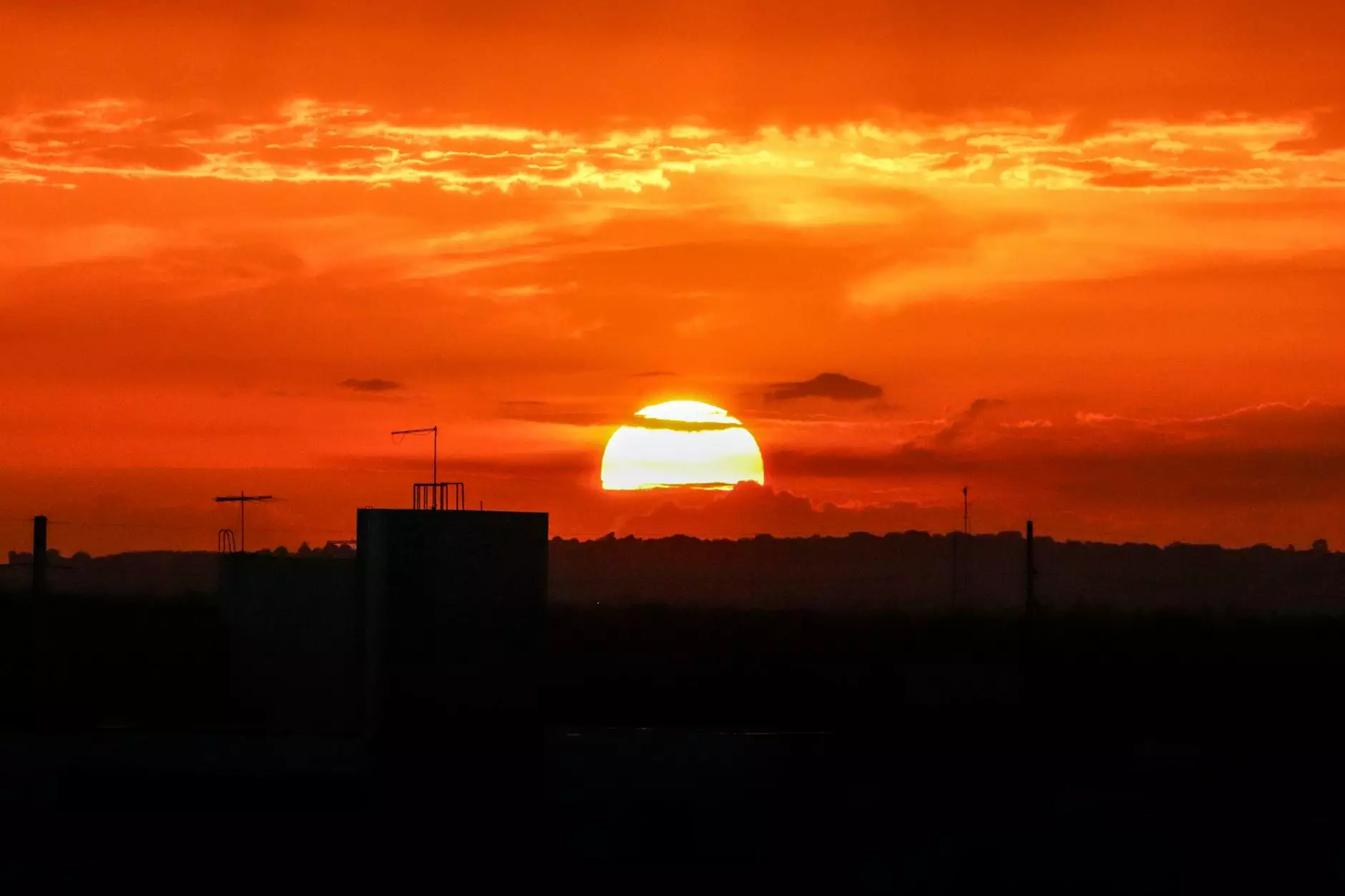
In the realm of modern manufacturing, PBF—short for Powder Bed Fusion—holds a prominent position, particularly in the field of 3D Printing. This cutting-edge technology utilizes finely powdered materials, which are selectively melted or fused to create highly intricate and robust parts. PBF is celebrated for its ability to produce highly complex geometries that traditional manufacturing methods cannot achieve. In this article, we will delve deep into the world of PBF, exploring its mechanisms, advantages, applications, and future prospects. Join us as we uncover how PBF is shaping the landscape of 3D printing and offering unparalleled solutions for industries worldwide.
What is Powder Bed Fusion (PBF)?
PBF envelops a group of additive manufacturing techniques where a laser, electron beam, or another fusion source selectively fuses powdered materials. This process occurs layer by layer, allowing the creation of parts that are not only lightweight but also possess superior mechanical properties compared to traditionally manufactured components.
Types of Powder Bed Fusion Technologies
- Selective Laser Sintering (SLS) - This method employs a high-powered laser to fuse particles of polymer, metal, or ceramic powders.
- Selective Laser Melting (SLM) - SLM utilizes a laser beam to completely melt metal powders, thereby creating highly dense materials.
- Direct Metal Laser Sintering (DMLS) - A variant of SLM, DMLS is tailored for metal powders, producing near-net-shape components suitable for demanding applications.
- Electron Beam Melting (EBM) - This technique uses an electron beam in a vacuum to melt metal powder, resulting in a fully dense component, typically used for titanium and cobalt-chrome alloys.
The Process of PBF in 3D Printing
The PBF process begins with a digital model designed using Computer-Aided Design (CAD) software. This model is then sliced into layers using specialized software, which prepares the instructions for the 3D printing machine. Here is an overview of how PBF operates:
- Layer Preparation: A thin layer of powder is spread over the build platform.
- Fusing: A laser or electron beam selectively fuses the powder according to the sliced model.
- Layer Recoating: Once a layer is completed, a new layer of powder is applied, and the process repeats until the part is fully formed.
- Cooling and Removal: After printing, the part is allowed to cool before being removed from the powder bed.
- Post-Processing: Many parts require additional finishing steps such as support removal, surface finishing, and heat treatment.
Benefits of PBF Technology in 3D Printing
The PBF process offers a multitude of advantages that make it a preferred choice for various industries. Below are some notable benefits:
1. Design Freedom
PBF allows for the creation of complex geometries that are impossible to achieve with conventional manufacturing techniques. Designers can create intricate structures with internal lattices or hollow sections, minimizing material usage and weight.
2. Material Efficiency
Traditionally, manufacturing methods often result in significant material waste. However, PBF utilizes only the necessary amount of powder needed to create a part, vastly improving material efficiency.
3. Customization
One of the most appealing aspects of PBF is the ease of customization. Each component can be tailored to specific requirements without significant redesign costs or time, making it an ideal approach for tailored medical implants and one-off components.
4. Mechanical Properties
Parts produced through PBF often exhibit superior mechanical properties compared to those made using traditional methods, such as casting. The quick cooling rates typically yield finer microstructures, enhancing strength and durability.
5. Rapid Prototyping
Speed is of the essence in today’s fast-paced market. PBF allows for rapid prototyping, significantly reducing the time from design to production and enabling quicker iterations based on testing and feedback.
Applications of PBF in Various Industries
The versatility of PBF makes it suitable for an array of applications across diverse industries. Below are some of the major sectors leveraging this technology:
Aerospace
The aerospace industry benefits immensely from PBF due to its ability to create lightweight, strong components. Critical aircraft parts, such as engine brackets and turbine blades, are being manufactured more efficiently using PBF, contributing to overall performance improvements.
Automotive
In automotive manufacturing, PBF is utilized for both prototyping and final production of components, particularly in high-performance vehicles. This technology enables the creation of customized parts while reducing the overall weight of the vehicles.
Medical
The medical field increasingly uses PBF for creating tailored implants, surgical instruments, and prosthetics. By allowing for bespoke designs that match a patient’s anatomy, PBF enhances both effectiveness and comfort.
Tooling
PBF technology is used to manufacture tooling components such as molds and dies. It reduces lead times and costs associated with traditional tooling methods while enhancing part performance.
Consumer Products
PBF is also making its mark in the consumer products industry, allowing for the rapid production of custom items ranging from eyewear to footwear, catering to the individual tastes of consumers.
The Future of PBF in 3D Printing
The future of PBF technology is incredibly promising. With ongoing advancements in laser power, scanning speeds, and software algorithms, the capabilities of PBF are expected to expand dramatically.
Emerging Materials
Research and development are underway to introduce new materials into the PBF landscape, including high-performance thermoplastics and biocompatible materials suitable for medical applications. This expansion will open up new opportunities across various sectors.
Integration with Industry 4.0
As industries move toward digitization and automation, integrating PBF processes with Industry 4.0 concepts is inevitable. Smart factories utilizing data analytics and machine learning will optimize production, reducing errors and enhancing efficiency.
Sustainability Initiatives
With growing environmental concerns, sustainability will be a central focus for PBF technology. Manufacturers will integrate more sustainable practices, such as recycling used powders and reducing energy demands, contributing to greener manufacturing solutions.
Conclusion
In conclusion, the world of PBF in 3D printing is a testament to the innovative strides being made in modern manufacturing. As technology advances and industries evolve, embracing PBF can lead to enhanced efficiency, reduced waste, and unparalleled customization capabilities. The integration of PBF technology into manufacturing processes signifies a leap toward the future, where producing complex, high-quality products becomes not just a possibility but a standard.
For more information on how PBF technology can transform your business operations, visit us at Infotron.